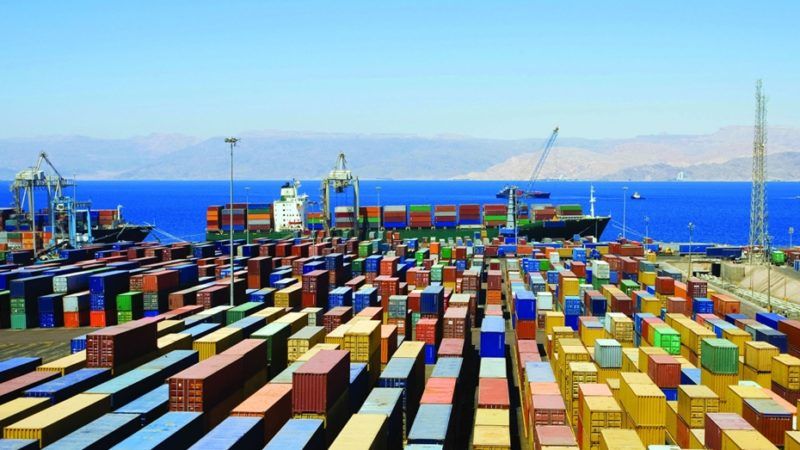
Push-back, almacenamiento ideal para centros de distribución
El Push-Back es un sistema de almacenamiento por acumulación que funciona con el principio LIFO (Last in, First out). Se considera un sistema de alta densidad, cuya operación de productos se realiza por lotes, con caducidad a mediano plazo, por lo cual es ideal para centros de distribución.
Por: Marta Bernal González
@bernalisima
El sistema push-back es una de las mejores soluciones para almacenaje en bloque, control de lotes y para maximizar el rendimiento de la operación.
Algunas de sus aplicaciones son utilizadas como preparación de expediciones, de producto acabado o en almacenes intermedios en proceso de fabricación de productos semielaborados. “Es muy popular en congelación o cámaras refrigeradas, pero se usa en sectores muy variados”, según Javier Martínez Fernández, director comercial de Polypal Colombia.
Para garantizar un mayor aprovechamiento de los espacios hay otros sistemas de rieles que forman parte del sistema de estanterías dinámicas, pero se utilizan basándose en el principio FIFO (First in, First out), primero en entrar, primero en salir. A diferencia del push-back, los otros sistemas requieren dos pasillos: uno de ingreso de carga, que es el de la parte trasera al rack, y el otro de salida, que es la parte del frente del rack.
El sistema de almacenamiento push-back se basa en el concepto de desplazamiento alineado de paletas. Funciona sobre una estructura fabricada con una leve inclinación y rieles que permiten la rotación de las estibas a medida que se van retirando con el montacargas.
La estantería lleva varios niveles y cada uno de ellos puede contener uno o más carriles paralelos. Sobre estos carriles están acondicionadas unas estructuras con ruedas, llamadas carros, a diferente altura para que puedan rodar en forma coordinada.
La acción comienza cuando mediante una carretilla o montacargas se deposita una primera paleta sobre el carro que se encuentra encajado dentro de la estructura, un poco más elevada.
La manipulación de las estibas en el momento de colocarlas sobre los carros se realiza con los patines inferiores dispuestos en forma perpendicular. Su mecanismo, basado en el desplazamiento de los carros con las estibas, entra a funcionar cuando, con la segunda paleta que se va a almacenar, se empuja la que se ha colocado previamente para que ruede hacia el fondo del carril. Como resultado de esta actividad, el siguiente carro queda al descubierto y sobre él se deposita la segunda paleta.
De la misma manera se procede con la tercera y cuarta estibas, dependiendo de la cantidad para la cual se ha diseñado la estructura. En general, la última paleta queda directamente almacenada sobre el carril de rodadura. Para retirar la mercancía, la acción de gravedad pasa a ser una gran aliada. Por lo tanto, al quitar la primera estiba con el montacargas, las otras paletas se desplazan hacia adelante quedando listas para ser extraídas.
DISEÑO
Dependiendo de las necesidades de los clientes, se diseña el sistema. La cantidad de niveles se define considerando el estudio previo en el que el diseñador considera el peso, el tipo de carga, las dimensiones de embalaje, la cantidad de referencias que se van a almacenar y el sistema operativo necesario para la manipulación de la mercancía.
El sistema también permite que en cada nivel puedan ir varios carriles, todo según las necesidades de almacenaje. Aunque en general la altura que se maneja es de doce metros, debido a que esta es la más alta posibilidad de manipulación con el montacargas, la máxima altura de almacenamiento “depende del montacargas, que debe estar preparado para empujar la carga en acumulación a la altura requerida”.
Para alturas elevadas, el montacargas deberá trabajar con mástil fijo en vertical para no alejar la carga de la estantería e inclinar las horquillas para adaptarse a la pendiente. “Evidentemente, ayudas como preselectores de alturas y cámaras son más que recomendadas”, afirma Javier Martínez Fernández.
La cantidad de paletas por nivel es definida por el diseñador, según la memoria de cálculo que presenta considerando los factores mencionados anteriormente. En algunos centros de cargas livianas emplean cuatro paletas por fondo de cada nivel. Hay opción de almacenar hasta seis tarimas en profundidad.
Por otro lado, la capacidad de carga de cada carro se basa en la capacidad permitida por el diseño y la memoria de cálculo que desarrolla el fabricante. Se maneja un promedio en cargas livianas de 1.200 a 1.500 kilos por carro. “En push- back de rodillos adaptamos el diseño a la estiba y al peso por estiba. En europaleta de punta es posible trabajar hasta con 1.500 kilos”, asegura el director comercial de Polypal Colombia.
Otra opción del mismo estilo de almacenamiento, tipo push-back, es la que funciona sobre una estantería que en lugar de adecuaciones para carros lleva rodillos. En este caso, los rodillos van colo-cados sobre largueros ligeramente inclinados hacia el pasillo, lo que permite el desplazamiento de las paletas que se encuentran ubicadas en el fondo al retirar la que se encuentra en la parte delantera. El movimiento en el caso de rodillos se realiza de manera controlada por frenos.
En el caso del sistema diseñado por Polypal, los planos dinámicos para cajas se aplican en diferentes versiones: sin presentadores, con presentadores rectos o con presentadores inclinados. Las parrillas (atornilladas) se componen de perfil de entrada, perfil de salida, perfil con “peine” de regulación para los caminos de roldanas y caminos de roldanas.
Cuando se realiza el diseño del futuro almacén es de suma importancia tener en cuenta los medios de transporte interno que se usarán, debido a que deben adaptarse a las dimensiones de las estanterías.

COMPONENTES
El sistema push-back consiste en una estructura conformada por bastidores, los cuales pueden ir soldados o con tornillos, con puntales, diagonales, travesaños y placas base.
Los bastidores pueden ser diseñados de acuerdo con necesidades especiales para zonas de riesgo sísmico, en diversidad de calibres y longitudes, según los requerimientos de almacenaje y con el fin de dar a la estructura mayor resistencia tanto a la torsión como a la carga axial.
Otro componente son los largueros, que se incorporan en el bastidor horizontal y van levemente inclinados para facilitar el desplazamiento de los carros. Sobre estos elementos se colocan los rieles y carros. Su diseño incluye placas, las que permiten controlar el movimiento de los carros para evitar un accidente.
Los racks pueden pintarse con diversos colores para facilitar la ubicación de la mercancía, especialmente cuando las estibas se encuentran ubicadas en niveles altos. De esta manera, quien manipula la mercancía no necesita manuales de ayuda o procesos de verificación de manera personal.
Adicionalmente, el sistema lleva topes de seguridad y de tarima que amortiguan el movimiento de los carros, tanto para cuando van en movimiento en la tarima como cuando llegan al final de las guías.
De la misma manera, la estructura tiene los elementos de rodadura asegurados a los lados para evitar el descarrilamiento, dispositivos de bloqueo y centradores que facilitan y orientan para colocar correctamente la paleta.
Los carros, fabricados con acero estructural, pueden soportar cargas superiores a los 1.200 kilos. Cada carro lleva cuatro ruedas de metal electrogalvanizado y canales estructurales que sirven de guía. Cada carro, además, puede tener un gatillo de seguridad para impedir el desplazamiento de la estiba, especialmente si no ha sido apoyada en forma correcta.
Según Javier Martínez, “para estibas es necesario trabajar con equipos que puedan empujar, como son los montacargas. Equipos como estibadores manuales o apiladoras son menos habituales, ya que su capacidad de empujar y la altura de trabajo son limitadas. En cajas se usa carga manual teniendo en cuenta la ergonomía y las limitaciones en cuanto manipulación de cargas por operarios”.
De igual manera, “cuando se trabaja con estanterías dinámicas es necesario usar estibas de calidad y en buenas condiciones. Como hay una gran variedad de estibas diferentes en el mercado es importante realizar pruebas con las estibas que se usarán en la bodega, para poder asegurar que el diseño del transportador de rodillos se adecúa a la estiba”, concluye Martínez.
VENTAJAS
Una de las grandes ventajas de este sistema es que solo requiere el mantenimiento de un pasillo frontal para realizar las operaciones de carga y descarga de los productos. Además:
- El tiempo de maniobra de las carretillas se reduce debido a que las distancias son mínimas.
- La temperatura de trabajo, en los carros, oscila entre los -30 ºC y 40 ºC.
- La capacidad de carga de cada carro permite superar los 1.200 kilos
- Comparado con otros sistemas, se considera que aumenta la capacidad de almacenamiento hasta en un 75 %.
- El sistema está diseñado para tener una alta densidad de almacenamiento mediante varios niveles y posibilidad de alcance en profundidad.
- Aunque el sistema de carros está diseñado pensando en el ahorro de espacio, la capacidad puede mejorarse con la implementación de una estantería con rodillos.
- Todos los componentes son de fácil instalación y existe la posibilidad de modificar la estructura.
- Facilita la posibilidad de almacenar diferentes referencias por nivel.
- Al usar este sistema, las empresas ahorran en equipos de manipulación de mercancía, debido a que básicamente se necesita solo un montacargas.
- Permite la rápida ubicación del material y facilita los inventarios.
- Los dispositivos de bloqueo y freno garantizan seguridad en el momento de realizar la carga y descarga.
- Es adaptable al espacio y utiliza componentes estándar.
- El rack push-back es de fácil mantenimiento debido a su proceso de fabricación de alta resistencia. El rodamiento no necesita lubricación.
- Permite un ahorro considerable en costos de operación.
DESVENTAJAS
- En comparación con otros sistemas, son riesgos menores; sin embargo, no dejan de existir debido a la manipulación de la carga, especialmente cuando esta se desliza por los carros o rodillos. Asimismo, pueden generarse daños en la estantería debido a la manipulación del montacargas en el momento de introducir las paletas en el sistema.
- Una desventaja puede presentarse debido a los costos iniciales, dependiendo del tipo de diseño que se requiera.
- No es sencillo, en caso de necesitarse, el cambio en la disposición del material.
- Aunque es posible, no es fácil realizar una modificación del sistema en general.
- Solo permite el almacenamiento de unidades homogéneas.
- Se presenta limitación en el momento de controlar fechas de caducidad.
VARIEDADES
El sistema push-back puede utilizar diferentes métodos de rodaje. En el mercado se encuentra el de rodillos, cuyo desplazamiento se realiza por la fuerza de la gravedad y da la posibilidad de colocar mayor cantidad de estibas.
Otro método es mediante carros, los cuales ruedan sobre rieles. La cantidad de carros (y estibas) depende de la estructura de la estantería.
El push-back está conformado por plataformas sobre las cuales descansan las unidades de carga y se van desplazando hacia adelante o atrás.

Fuente: https://revistadelogistica.com/almacenamiento/push-back/